Tid
1.5.2023–30.4.2025
Projektägare
Åbo yrkeshögskola
Samarbetsparter
3D-printing (3DP) is a relatively new additive manufacturing technology that has revolutionized industrial mechanical design by facilitating highly customizable and lightweight products and rapid prototyping. Recently, 3DP has been observed to be a potential disruptive technology also in the pharmaceutical industry. Indeed, 3DP facilitates the use of multicomponent materials and complex geometries, which are difficult to manufacture with conventional methods, and which are potential both for better one-fits-for-all products (e.g., better efficacy, less side-effects), and for personalized medication. The developed materials and structures also make it possible to develop drug products with better patient-compliance. Individual doses, several active pharmaceutical ingredients (API) in the same product, and customization of release rates and profiles of API according to the needs of the patient both for short and long-acting administration, are possible with 3DP based manufacturing.
Despite the promising prospects, the pharmaceutical industry has identified several needs and challenges related to 3DP. First, adapting existing medical grade materials and so-called medical grade -capable materials for 3DP and development of new materials, also multicomponent materials; the existing materials are not good enough for all types of API, dosage forms or for long-acting release, and new materials must be safe and non-toxic. Second, regulatory authorities, such as FDA and EMA, anticipate that new regulation is needed for 3D-printed drug and combination products (e.g., drug and a medical device for controlled drug delivery). The regulatory authorities think that 3D-printing opens a lot of possibilities to make better drug products, both for one-fits-for-all and personalized products, but new regulation is needed because there are risks that are unique for 3D-printing as a manufacturing method. These risks must be understood, quantified and addressed when planning research and product development by 3DP. Their mitigation requires new real-time/online monitoring technologies (e.g., photoacoustic spectroscopy) and better predictive knowledge about rheological behavior of materials, available e.g., through numerical simulations. Third, to utilize the full potential and flexibility of 3DP in the pharmaceutical industry, the full transport path of the substances, from raw materials, through 3DP, to the patient must be understood and controlled. This requires numerical models (e.g., dissolution, rheology and fluid flow, production) and digital twins that facilitate inverse design of medication starting from the patient, robust control of production, and quality control through quantification of uncertainties. It also requires practical development of the 3DP process and equipment, e.g., automation, sensors, heating, raw material feed systems, tailored for pharmaceutical applications.
Key findings
– Testing and development of new (multicomponent) medical grade materials, formulation processes and products specifically tailored for 3DP;
– Digitalization of the drug development process by accurate numerical models of material transport and 3DP production, addressing quality control and uncertainty;
– Definition and testing critical material attributes and critical process parameters to identify critical quality attributes for the 3DP products and defining their quality target product profiles;
– Analyzing and following the regulatory landscape for 3DP medicinal products to anticipate future regulations on research and product development of 3DP medicinal products;
– Testing and development of PhotoAcoustic Spectroscopy (PAS) for online process monitoring to validate (and eventually control in near real-time) the end-product quality.
As facilitated by the highly customizable digital manufacturing technology (3DP), this research project addresses the entire chain from raw materials to the patients (population).
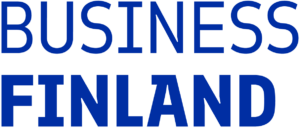
Kontakta oss
Jessica Rosenholm
Professor
i farmaci företrädesvis läkemedelsutveckling
Farmaci
Tfn +358 504605886
Chunlin Xu
Professor
in Fiber and Biopolymer Chemistry
Laboratoriet för naturmaterialteknik
Tfn +358 440362088