16.12.2021
Hos Sandvik i Åbo designas och tillverkas världens mest avancerade dumprar och lastare för gruvdrift. Gruvbranschen håller både på att bli elektrifierad och automatiserad.
Framtidens gruva är elektrisk – det är en tes hos Sandvik Mining and Rock Solutions, världsledande tillverkare av gruvmaskiner. Sandviktillverkad utrustning finns över hela världen och varumärket är bekant för alla som jobbar inom gruvbranschen.
– För att vara ett företag med en omsättning på cirka en miljard euro och 2 400 anställda i Finland är vi ändå relativt okända för den stora allmänheten, säger Mats Eriksson.
– Att industriledande tunga gruvtransport- och lastfordon görs i Åbo är förmodligen också rätt okänt för åbobor i gemen. Däremot känner folk i gruvbranschen till Åbo tack vare våra fordon.
Mats Eriksson är verkställande direktör för Sandvik Mining and Construction. Han är alumn från ämnet informationsteknik vid Åbo Akademi och har en lång internationell karriär bakom sig. Karriären innehåller längre vistelser i olika länder i Europa och i Asien (Kina, Korea, Singapore) och han har även startat och lett verksamhet i Brasilien och i USA. Hos Sandvik i Åbo har han varit sedan 2016.
– Mina studier på Åbo Akademi var som sagt i informationsteknik. Min karriär formades dock på ett sätt som gjorde att jag behövde helt andra färdigheter. Men jag har alltid varit intresserad av att lära mig nytt, och det gör jag även hos Sandvik. Jag visste ingenting om gruvdrift och gruvdriftsteknologi innan jag kom hit men jag hade mycket erfarenhet av att bygga och leda internationella organisationer.
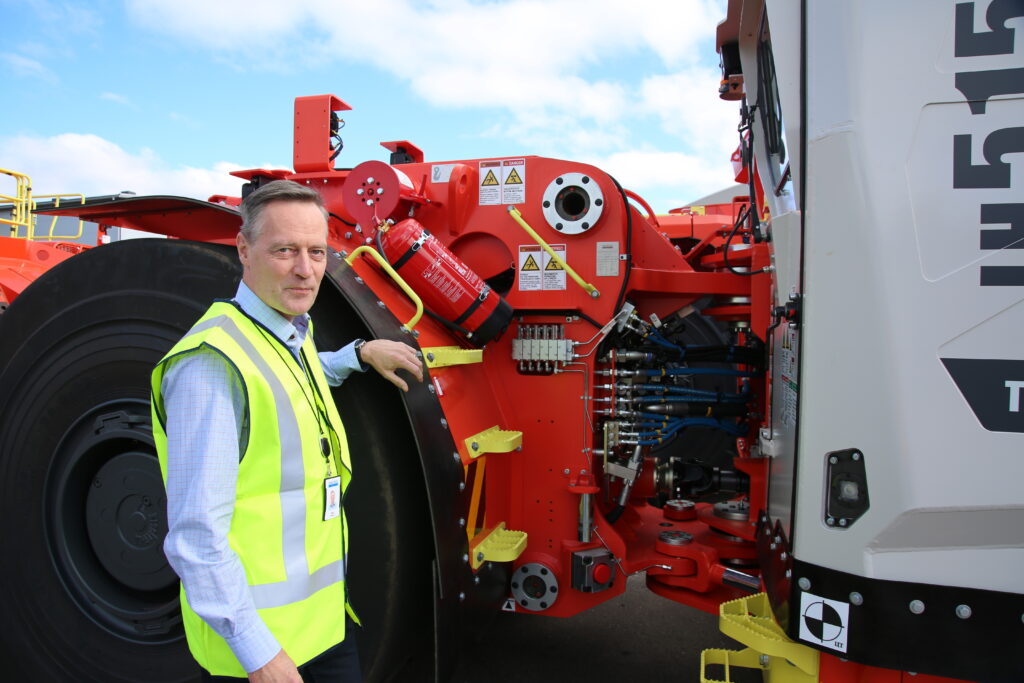
De modernaste gruvorna idag är om inte helt elektrifierade så redan till stora delar automatiserade. I Åbo designas och tillverkas de upp till femtio ton tunga förarlösa lastare och dumprar som kör upp material från gruvschakt i hela världen. Fordonen är utrustade med laseravläsare som gör en tredimensionell modell av schaktet dumpern rör sig genom; maskinen känner den exakta texturen på gruvväggarna, en textur som för ett mänskligt öga kan se identisk ut meter för meter men variationerna är unika och därför kan dumpern bestämma sitt läge noggrant. GPS fungerar inte ett par kilometer under markytan (radiosignalen når inte fram). Dåligt fungerar det också med dieselångor i slutna utrymmen. Bland annat därför består upp till sjuttio procent av kostnaden i en underjordisk gruva i utgifterna för ventilationssystem, och därför finns det ett starkt incentiv till att konstruera eldrivna maskiner framom dieseldrivna. Ett alternativ till diesel, som är i bruk sedan länge, är eldrivna lastare som förses med ström genom en kabel lastaren släpar efter sig genom gruvan. Men det säger sig självt att den grova kabeln är något man gärna slipper. Då är självburna batteripaket lösningen – det vill säga väsentligen samma typ av lösning som hos elbilar. Dessutom kan en dumper inte fungera med kabel eftersom sträckan den kör är för lång, och det innebär att problemet med avgaser och ventilation bara delvis löses med att använda kabel-lastare
– I designen av eldrivna maskiner räcker det inte enbart att ersätta dieselmotorn med en elektrisk motor, säger Eriksson.
– Eller det är det bytet av motorer som är generation ett i utvecklingen. Men en komplikation som man snabbt stöter på är att man med ett batteri inte har en kontinuerlig kraftkälla på samma sätt som hos en dieselmotor eller med en kabel som förser maskinen med el.
Med ett batteridrivet fordon vill man därför gärna förlänga längden på arbetstiden innan batteriet behöver laddas eller bytas. Det ger oss en anledning till att minimera alla moment som förbrukar mer energi än de behöver och också en anledning till att inte heller hålla igång system när de inte behövs. Effektivering betyder att olika komponenter byts ut och att man försöker se till att olika processer i maskinen effektiveras. Hit hör till exempel att effekten på hydrauliken reduceras till en mindre energiförbrukande nivå och att fläktar ställs om så att de bara är i gång när avkylning behövs och inte kontinuerligt, och så vidare.
Effektiviseringen är generation två. Sandvik har däremot tagit ett steg längre och tänkt om hela designen och utgått från elmotorer och batteripaket som grundläggande delar och byggt fordonen kring dem. Då försvinner kraftöverföringsaxlar, växellådor och andra moment som inte behövs med elmotorer. Det här är ett liknande koncept som Tesla startade, det vill säga: motorerna är flera och finns direkt bakom hjulen.
– Våra konkurrenter utnyttjar den andra generationens lösningar medan vi är ensamma om att tillämpa det här som vi kallar generation tre. Vi är gruvmaskinernas Tesla.
Eriksson bedömer att Sandvik har ett cirka två års försprång i teknologi, men det är ett försprång som konkurrenterna snabbt försöker nå ikapp. Därför måste även Sandvik förnya sig kontinuerligt med egna innovationer och patent. En sådan innovation är sättet på vilket Sandviks dumprar och lastare självständigt kan byta sina batteripaket utan att varken lyftkran eller mänsklig inblandning behövs – en detalj som gör hela systemet med batteridrivna fordon både mindre komplicerat och mera effektivt. Man är tvungen att byta batterier för i gruvor ska maskinerna vara igång 24/7 så långt som möjligt. Maskinerna kan inte stå stilla för att de ska laddas.
Orsaken till att gruvbranschen inte kastat sig över batteriteknologin tidigare beror dels på det dyra utvecklingsarbetet, dels på att tekniken måste gå att reparera på plats i gruvan utan att maskinen behöver sändas tillbaka till tillverkaren, dels på att batteriteknologin är anpassad till bilindustrin, och dels på grund av brandsäkerheten. Brand som äter syre och genererar värme är tillsammans med elavbrott och översvämning något man mycket ogärna vill ha i en gruva. De batterier man valt till gruvmaskinerna är därför litium-järnfosfatbatterier istället för litium-nickelbatterier (som mestadels används i bilar).
– Litium-järnfosfatbatterier har lägre energitäthet jämfört med litium nickelbatterierna (det vill säga mindre effekt per kilogram batteri, red.). Men det man istället får är batterier som är brandsäkrare.
I en video från ett säkerhetstest kan man se hur ett järnfosfatbatteri kan penetreras utan att explodera och utan att tappa spänning. Nickelbatteriet exploderar däremot och brinner intensivt om det penetreras (ett inte omöjligt scenario i en mindre gruvolycka, som med ett brinnande batteri kan bli en stor olycka). Men järnfosfatbatteriet är alltså tyngre än nickelvarianten. Eriksson säger att det naturligtvis vore bättre om batteriet vore lättare, men att man med det tunga batteriet kan använda batteripaketets massa som motvikt på Sandviks lastare. De batteridrivna lastarna har samma yttre dimensioner som sina systermodeller som drivs med diesel. De är dock betydligt tyngre än dieselversionerna, på grund av batteripaketets tyngd, men elmotorerna ger å sin sida dubbelt mera effekt (hästkrafter) än dieselmodellerna. Det betyder att de batteridrivna dumprarna och lastarna både klarar av mera last och högre fart samtidigt som det inte finns kraftöverföringssystem (axlar och växellådor) som läcker energi och slits på samma sätt som i versioner med förbränningsmotor.
– Allt pekar på att vi kommer att gå till en genomgripande omställning mot eldrift. Och att den så motståndslöst kommer att bli av är för att industrin själv driver omställningen, säger Eriksson.
Även om Sandvik gärna använde batterier tillverkade i Finland tar man just nu sina batterier därifrån man får dem, gruvindustrin är en marginell köpare av batterier jämfört med bilindustrin.
– För mig är det viktigt att få vara med i den här processen då vi övergår till hållbarare teknologi. Det skulle verkligen inte kännas lika motiverande att vara med om det vore tvärtom.