5.6.2018
Jyri-Pekka Mikkola has made a major technological breakthrough that will make it possible to make copies of fossil fuels out of sugar. The next challenge is to have it replace an established industry.
“Ten years ago, I decided that I wanted to change the world.”
Jyri-Pekka Mikkola, Professor of Industrial Chemistry and Sustainable Chemical Technology at Åbo Akademi University and Umeå University, has taken a major step toward achieving his goal. The first patent for producing exact copies of fossil fuels without requiring a single fossil component has already been approved. The dream of making it possible to power existing engines with carbon-neutral fuels has, in other words, already been realised.
The next step is to actually power all engines with carbon-neutral fuels. This is an enormous challenge. When you take on a massive, powerful, rich and established industry like the petroleum industry, you are going to meet some stiff resistance.
But Mikkola is unwavering in his belief that it can change the world. We actually have no choice.
“You have to be very careful when collaborating with all the traditional petroleum corporations. Once they understand what’s at stake, they’ll buy up all the rights to it and lock it away,” says Mikkola.
“Time will tell how things play out, but if we don’t succeed, someone else surely will. The patent was drafted by a patent attorney in such a way that it won’t be possible to figure out how the fuel is made right away, but if you’re patient, you’ll be able to figure it out. As said, it takes around ten years. This was really hard – the hardest thing I’ve ever done in research.”
Sugar power
Mikkola’s breakthrough makes it possible to produce hydrocarbon-based fuel out of various sugars, which can be found in all types of biomass. This means that petrol, diesel and jet fuel can be made using forest residue, sawdust, sugar beets, food waste, farming waste or cakes from sewage treatment plants.
The process begins with hydrolysis, which involves adding sulphuric acid and letting the lignocellulose in the biomass to disintegrate, a step that is unnecessary when the raw material is sugar beets or sugar cane. Then, the sugar is fermented to form alcohol—primarily ethanol—but all types of alcohol will do.
The ethanol and water mixture is then run into the reactor system, which consists of two 1.5 metre long pipes that contain extremely complex catalysts. A catalyst increases the rate of chemical reactions without being consumed itself.
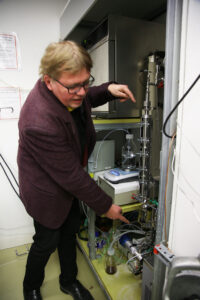
“There are thousands of different types of catalysts in the world, but ninety per cent of everything we eat, stand on, wear and see is produced by means of heterogeneous catalysis,” explains Mikkola.
“To put it more simply, catalysts are solid materials, powders—in many cases metal oxides or activated carbon—which have an extremely large surface area. The surface is full of microscopic pores, which often contain nanoparticles spread throughout the pore system. A single catalyst grain can have a surface area equal to two football pitches, which is approximately 2,000-3,000 square metres per gram.”
The development of catalysts has been the biggest challenge in Mikkola’s research.
“The whole secret to most chemical industrial processes can be found in catalysts. I won’t—in fact I can’t—explain how our catalysts are formed because they are so complex.”
Catalysts need heat to get reactions started. However, because certain reactions generate heat while others require it, the process is automatic once it is up and running.
Out of the reactor comes a high-quality fuel.
“We end up with a pure alkylate petrol and light carbohydrate (propane-butane gas). We also get more water out of the reactor than we put in, i.e. synthetic water,” explains Mikkola.
“Water isn’t a major issue in the Nordic countries, but when you bring Southern Europe—not to mention Africa, the Middle East and Asia—into the equation, water takes on a whole lot more meaning. Even though we do lose hydrogen atoms in the process, it doesn’t matter, because the water is almost worth more than the petrol.”
With a double-reactor system, Mikkola can currently produce approximately 250 litres of fuel a day. The quality of the fuel has been tested by Seabolt in Gothenburg and Shell in Rotterdam, easily meeting the requirements set in EU fuel standards. For example, its benzene concentration, which must be below 100 ppm (parts per million), is 2 ppm and its octane rating is over 100, which is far better than the fuel you’ll fill up with at your average petrol station.
Top secret
The research was conducted in a cottage in a rural district of Västerbotten, Sweden. The researchers involved worked on double projects, with one project being published and the other dealing with the new patent.
“When you’re working on a completely revolutionary technology that will irrevocably change the playing field, you have to be extremely careful and keep everything under wraps the whole time. Everything was kept secret,” says Mikkola.
“It’s been our long-standing practice to have everyone leave their phones outside the room when we hold meetings. Nokia was already doing this in the 90s. And, whenever working with sensitive information, the computer being used must not have any Internet connection. That’s the reality we live in today.”
Interest in the new invention has been huge since the patent was published. Mikkola’s email is subjected almost daily to intrusion attempts by hackers and his phone is ringing constantly. People want to know how the invention works and how they can invest in it.
For the time being, there is no clear idea as to what type of financing approach will be used. One thing is sure: enormous investments will be necessary to restructure the way fuel is currently produced.
“Just on Swedish highways alone, around 15 billion litres of fuels are consumed each year. Then, on top of that, you have air traffic. And it’s going to get worse. In his book and last TEDtalk, The Global Population Growth, Hans Rosling said that, according to statistics, nine out of every ten flights are made in the old Western world. In 20 years, nine out of every ten flights will be flights in Asia,” explains Mikkola.
“We now have a functional technology, but the problem is that we need an enormous amount of metal to produce and store the fuel. In order to put together all the pipes, reactors and storage tanks needed to satisfy the demand for fuel, we would need so much metal that it will cost astronomical sums of money.”
One possible solution that Mikkola is now working on is to keep fuel production local in smaller quantities, in small reactors inside containers.
“Containers can be transported anywhere in the world. Then we’ll have smaller facilities that can be run by another operator and, bit by bit, we’ll reach our goal,” says Mikkola.
“It’s an appealing alternative. When you have a local village council or a hauling firm that buys a container, or an outfit running a pulp mill with excess heat that can be used to start the process, or a sawmill with plenty of sawdust at its disposal, it becomes possible to set up a fermentation plant to produce ethanol and run the plant according to the same integration of various processes.”
A common problem encountered in the development of alternative fuels seems to be the requirement to modify engines. But, this isn’t a problem with your method, because the fuels it produces are exact copies of the existing fuels, right?
“That’s right. Plus, we don’t have to build a massively complex processing facility like an oil refinery, which consists of millions of individual operations. While an oil refinery costs at least 1.5 billion euros to build, our method makes it possible to set up distributed production in smaller plants. This eliminates a large amount of the transport costs and we end up with an identical product without a single drop of oil.”
“If we take an established competitor like Neste, they still use tonnes of fossil hydrogen gas in their NEXBTL diesel. This comes from natural gas. We have exact copies of fossil fuels that don’t contain a single fossil molecule. Because sugars are the most common biological raw materials, they’re the most easily available raw materials there are.”
How much raw material is needed to produce the fuels?
“Sweden uses around 15 billion litres of fuel on its highways each year and Finland around half that, say 8 billion litres. According to our rough calculations, this is equivalent to perhaps 6 billion kilograms. I would say that, if we include the required amount of sugars, we would need almost 20 billion kilograms of sugars.”
In my mind, that seems like an impossibly large figure.
“Yes, that works out to 20,000 million kilos of sugars.”
In 2016, a total of 106 million cubic metres of trees grew in Finland. According to a very rough estimate, this would provide approximately 24,000 million kilograms of sugars, which would today be classified as ‘utilisable’. When financial profitability and available surplus from the forest industry are included in the equation, the amount needed drops to around 10 per cent.
“Raw materials have to come from an extremely wide variety of sources. We have to be much, much better at making use of the circular economy.”
Next up: the fertiliser industry
Jyri-Pekka Mikkola, ten years of work has produced results. Are you satisfied now?
“No. I won’t be satisfied until this is out on the market. And, I already have the next big thing in my sights, something we’ll be tackling as soon as we can.”
“It involves solving the problem of nitrogen oxide emissions from diesel fuels. The current approach is stupid—I have a much better idea. Nitrogen oxides are partially linked to another problem, which has to do with global food production, i.e. the nitrogen industry and the ammonia and nitric acid needed to make fertiliser.”
“The Haber-Bosch process fixes nitrogen from the air. 70 per cent of the world’s population and domesticated animals wouldn’t exist if we didn’t have this, but the process has a major problem: it requires precious metal catalysts and the entire process revolves around and runs at temperatures in the thousands, not to mention being powered by natural gas and oil. So, this is the kind of industry I want to attack next.”
You don’t really deal with small industries, do you?
“No. Politicians deal in trivialities and their solutions often take us from the frying pan and put us smack dab into the middle of the fire. For example, the electric car is really not a solution. According to a lifecycle analysis, a battery-powered car is at least 30 per cent worse than a normal petrol-powered car.”
“This is due to the fact that we have to mine lithium ore, most likely in Argentina or Chile, where the biggest deposits are found. Then, you have to crush all that rock. How much does that cost in energy? Then, the ore has to be shipped to Japan for electrolysis, which also requires a massive amount of electricity to produce lithium metal. There is no other electrolysis method for reducing lithium oxide to lithium metal. Then, the metal has to be shipped—possibly to Korea—to make batteries.”
“And, yes, we should not actually be talking about lithium batteries, but cobalt batteries. Cobalt is the deciding factor. Where does cobalt come from? Almost exclusively from the Congo, where it is produced using child labour. The batteries last around ten years. Then, they degrade and need to be recycled, which is extremely difficult—and there we have electrolysis again. It is an extremely difficult and energy-consuming process to recycle metals and put them back into circulation. Battery-powered cars are a monumentally bad idea when you look at their lifecycle analysis. A battery-powered car creates more emissions than a petrol-powered car.”